Power of coal-laboration
Minnkota and BNI Coal have been building a stronger relationship around optimizing plant and mine practices – and it’s paying off.
The ease with which Wade Boeshans and Craig Bleth teasingly recount a missed breakfast meeting makes them sound like boyhood friends – not the ones leading the show at BNI Energy and Minnkota’s Milton R. Young Station.
Boeshans and Bleth, president and general manager of BNI Energy and Minnkota senior manager of power production, respectively, have grown close over the past few years. The bond is a part of the companies’ recent joint initiative to build a stronger partnership for streamlining processes, eliminating redundancies and achieving lower total costs for the joint enterprise.
BNI Coal and Minnkota have been solid power partners for 50 years. But in a 2016 discussion between Boeshans and Minnkota CEO Mac McLennan, the leaders recognized they were entering an era of new challenges facing their facilities, their operations and the industry.
“BNI and its mining operation and this plant are ultimately co-destined,” Boeshans said. “Our futures are tied together. There is no ‘one wins, one loses.’”
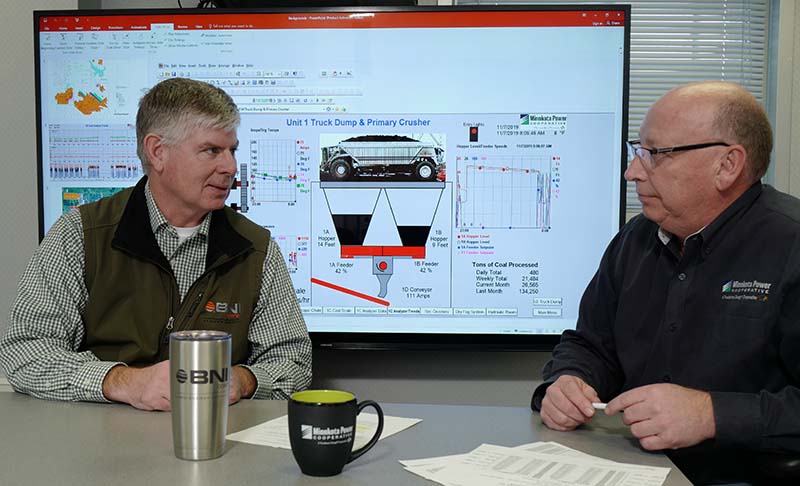
The companies joined each other at the table and began to develop a cosponsored mine optimization plan, taking ideas from every level of the organizations.
“We were looking at ways to increase efficiencies, focused on saving money,” Bleth said of those early planning days. “We acknowledged that BNI has certain strengths that we could utilize, like their work with heavy equipment.”
“The response from the team was phenomenal, in terms of the openness of thinking and the types of opportunities that were brainstormed,” Boeshans said. “Over three to six months, we identified a set of initiatives that we were able to work together on to integrate into our respective operations.
“We realized, boy, we can do great things together,” he added. “It evolved in that way.”
Coal delivery examination
The details of the plan took hold in 2018. The companies laid out their optimization agenda – modifying the coal delivery and plant feed process; reclaiming and expanding the coal stockpiles; and finding ways to share equipment, services and knowledge.
One of the first projects was coal delivery. “That ultimately was the lowest-hanging fruit that wasn’t identified by me or Mac or Craig, quite frankly,” Boeshans said. “It was the guys who were in the trenches and managing this day-to-day.”
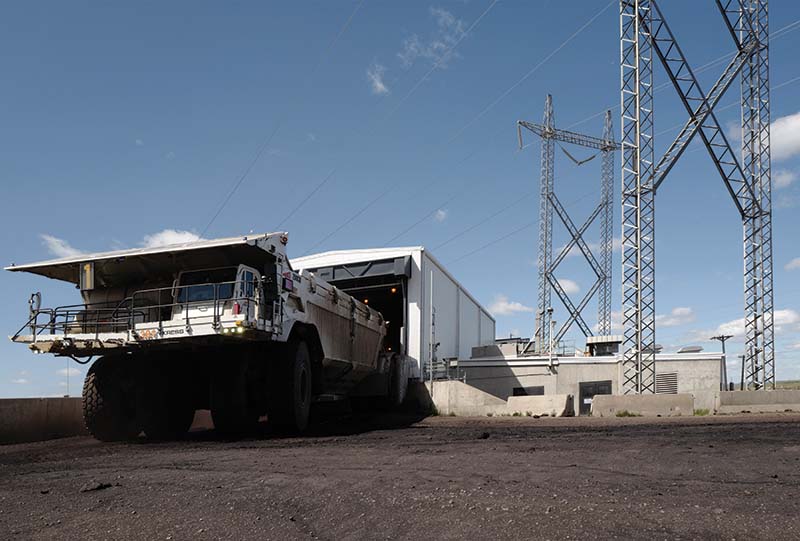
The idea came from BNI’s newly promoted production manager, Mike Heger, who realized that if weekly coal deliveries to the Unit 1 and Unit 2 generators were sequenced differently, efficiency would improve significantly.
“He modeled it all out, brought it to this optimization team and presented it there. We looked at it and said, ‘That’s really cool,’” Boeshans recalled.
The changes have allowed BNI to move from delivering 250-280 tons of coal per truck hour to 320 tons, creating a potential annual cost reduction of $1-2 million.
Active stockpile expansion
The team uncovered another money-saving collaboration long-buried in the mine – a million-ton field stockpile of coal that was established more than three decades ago for insurance against major events (weather, mechanical or labor related) that could interrupt coal deliveries to the plant.
Company leaders felt their proven delivery reliability had eliminated the need for that level of inventory, and that it should be reclaimed and replaced with an expanded, readily available stockpile right next to the plant. The size of the plant’s active coal stockpile increased from 60,000 tons to 250,000 tons.
“The costs for mining the field coal stockpile were incurred long ago. What’s left is the load and haul costs, which results in a cost reduction to us,” Bleth said. Recovering the coal and reclaiming the area also eliminates a future reclamation liability.
The stockpile expansion started in 2018 with permitting, regulatory approval and engineering. Minnkota moved power lines in the spring of 2019 to allow for the expanded active stockpile and major excavation dirt work was completed in September. By the end of October, BNI started to add coal to the new, efficient stockpile.
Overall, Minnkota and BNI estimate the stockpile adjustments will create $3-6 million in cost reductions over the five-year timeframe in which they reclaim the pile.
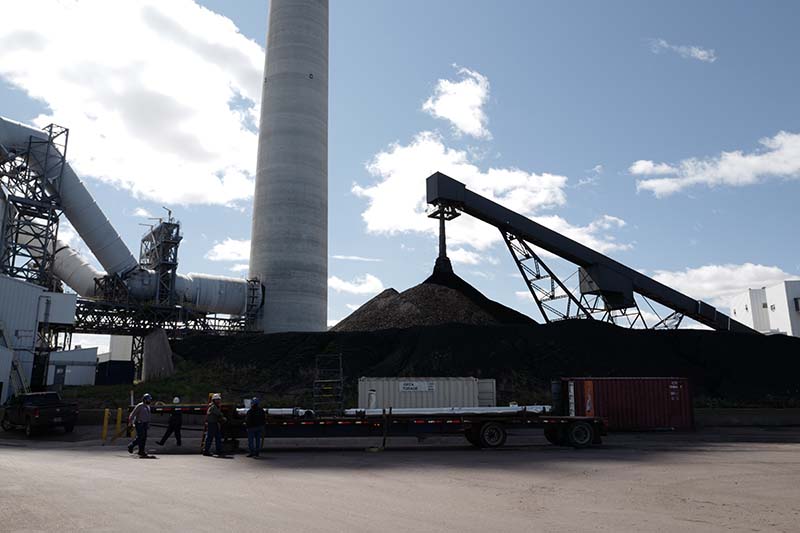
Shared equipment and expertise
The committee then examined the companies’ resources and determined BNI had heavy equipment maintenance capabilities and expertise that Minnkota could use. While Minnkota has six pieces of heavy equipment, such as haul trucks, bulldozers and loaders, BNI has more than 50. Until this year, Minnkota had been paying an outside company to perform its preventative and breakdown maintenance. Allowing BNI to work the equipment into its maintenance rotation would be achievable and more cost-effective.
“One way or another, we pay for the work. But when we pay BNI for the work, there is a return on the other side, since the mechanics’ time on our equipment is deducted from the cost of coal,” Bleth explained. “It’s almost like getting the work for free. Those are the kinds of things Wade understood for a while, but it took time to get us all to understand,” he added with a laugh.
“It took a while to understand the accounting together,” Boeshans replied with a smile.
The team also recognized some equipment redundancies between the mine site and the plant site.
“We have the exact same front-end loader. We use it less than 10% of available hours, but we need it to run our businesses,” Boeshans said. “So we decided to just share one loader between us. That’s just one example of the ways in which we can share equipment and expertise between our two organizations.”
Minnkota and BNI have also put their brains together to develop better coal-handling and blending processes and share earthworks projects. They will continue toseek other opportunities as the optimization initiative moves forward, using both state-of-the-art data analytics and old-fashioned teamwork to preserve their co-destiny.
“All of this is a part of what we already do. We get together and we figure things out,” Boeshans said. “That was, to me, one of the biggest values of this initiative – the relationships that were built over the common goal of working together.”
...