After a 12-hour shift keeping a watchful eye on the region’s electric grid, Troy Tretter goes home and starts his new routine. In his garage, he applies a healthy dose of hand sanitizer. Once inside, Tretter’s clothes go directly into the laundry and he heads straight to the shower. Finally, he’s able to greet his wife, 2-year-old son and newborn boy who was brought into the world in the midst of the coronavirus pandemic.
It’s a world that has changed significantly – and, in some ways, permanently – during the last two months due to the spread of the virus. Businesses have closed or significantly altered operation. School is being conducted almost exclusively online. Many social gatherings have been canceled or postponed.
“It’s definitely made us all be more cautious,” said Tretter, a power system operator. “We’ve been doing grocery pickups and things like that rather than going into the stores. It makes you think twice before going out in public.”
Still, the power must stay on. As an electricity provider, Minnkota is classified as an essential business that can never truly close. Unprecedented actions have been taken to protect the safety and health of the cooperative’s 400 employees. Since mid-March, most of the office staff have been working from home, while outside crews and power plant personnel have been split into smaller, separate crews to accommodate increased social distancing and sanitization.

Tretter is a member of the team that monitors the reliability of the electric grid 24 hours a day. Each power system operator sits alone in a room surrounded by digital monitors displaying colored lines and blinking lights – each of which represents a connection to reliable electricity for homes, essential businesses and hospitals during the pandemic. It’s a job that requires months of training, ongoing education and federal certifications.
“It’s in the back of your head that there are only a handful of people who can do your job,” Tretter said. “We want to be as safe as we possibly can be.”
While the group is already in a highly secure area separated from the rest of the workforce, additional social distancing and disinfection precautions have been taken to help protect the group from spreading the virus. The power system operators are never together in the same room – a protocol that requires detailed communication.
“We have to really be sharp in our documentation of everything we’ve done during the day and pass that information on to our replacement,” said fellow power system operator Aaron Bjerke. “There’s no room for error. You have to be focused and diligent and make sure that you have all the information in front of you. One misstep and people are without power.”
Building a team
Storms, cyberattacks, system malfunctions – Minnkota has emergency plans in place for these and many other industry crises. A pandemic presents a different challenge. In early March, the cooperative formed a pandemic preparedness team representing all employee divisions. The team meets throughout each week via conference call to assess the ever-changing situation, implement procedures and keep the lines of communication open with the entire workforce.
Some of the first steps taken were to significantly upgrade cleaning services, provide higher-grade disinfectants and develop cleaning protocols in the event the virus is contracted by an employee.
“We’ve tried to flood the workplace with all the available cleaning tools that we might need,” said Jason Uhlir, corporate services manager and pandemic team member. “The amount of cleaning that’s being done is very visible.”
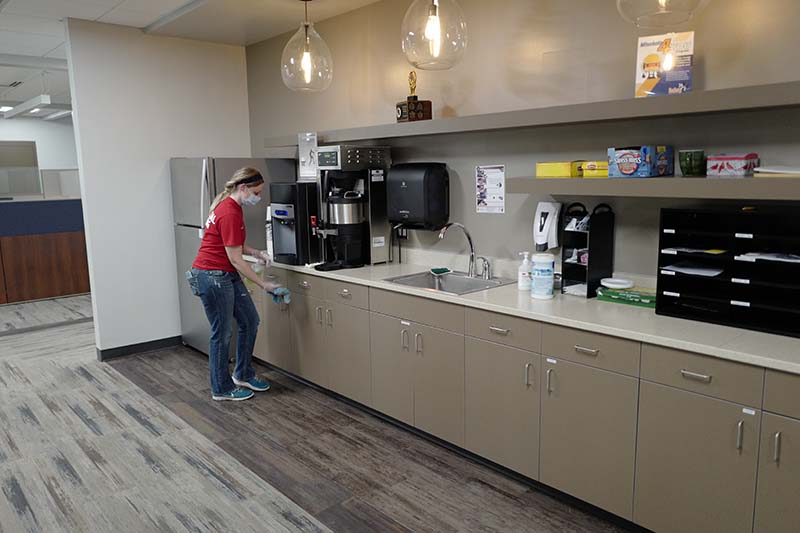
All common workspaces and frequently touched items, like door handles, are being routinely sanitized using hospital-grade disinfectants. Cleaning stations have been strategically set up for employees to further address personal workspaces – whether it be an office desk or a work truck. Minnkota has even purchased a disinfectant fogging system to provide an additional level of sanitization.
“It’s meant to be used as a complement to traditional cleaning and disinfection,” Uhlir said of the fogger. “We have hard-to reach areas that aren’t easy to wipe down, like shared forklifts, tools and large pieces of equipment.”
Minnkota’s procurement department has worked to ensure the cooperative has access to all materials during the pandemic – from hand sanitizer bottles to steel for substation construction.
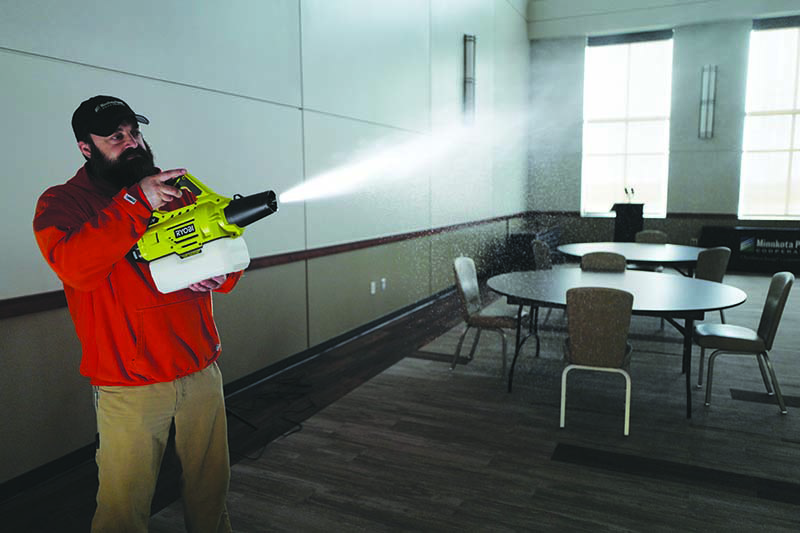
Safety among the distractions
Power plant personnel and power delivery crews have continued to report to work, albeit in smaller, separate crews to limit the amount of employees on site and to allow for greater social distancing.
In addition to health concerns, COVID-19 has created an undeniable amount of distractions. Safety communication has been prominent to ensure employees are working to protect themselves and their co-workers from on-the-job hazards.
“Everyone from our leadership team all the way through the rest of our workforce has kept safety at the forefront,” Uhlir said. “It’s important to have those continual reminders during these times of different work schedules.”
At the Young Station, maintenance crews are typically scheduled for day shift, with only two mechanics on an evening shift. Now, there is a fairly equal day and night shift. Face-to-face overlap that had previously been typical for communication purposes has been discontinued, and that communication is taking place in other ways.
“We used to have crossover time between shifts; now we don’t even want them to see each other,” said Ross Ford, plant maintenance superintendent. “That extra time allows us to clean work areas, community tools, keyboards – everything.”
The days of filling conference rooms for morning briefings have been replaced by phone calls and video chats. As challenges arise on projects, emails are becoming the new standard.
“You used to walk down to the work area and show the person what you needed,” Ford said. “Now that has to be communicated through an email.”
Additional safeguards have been put in place at the Young Station to isolate employees from business-critical contractors. The contractors and employees now have separate entrances, bathrooms and break areas. If work needs to be conducted that makes social distancing a challenge, proper personal protective equipment (PPE) is required.
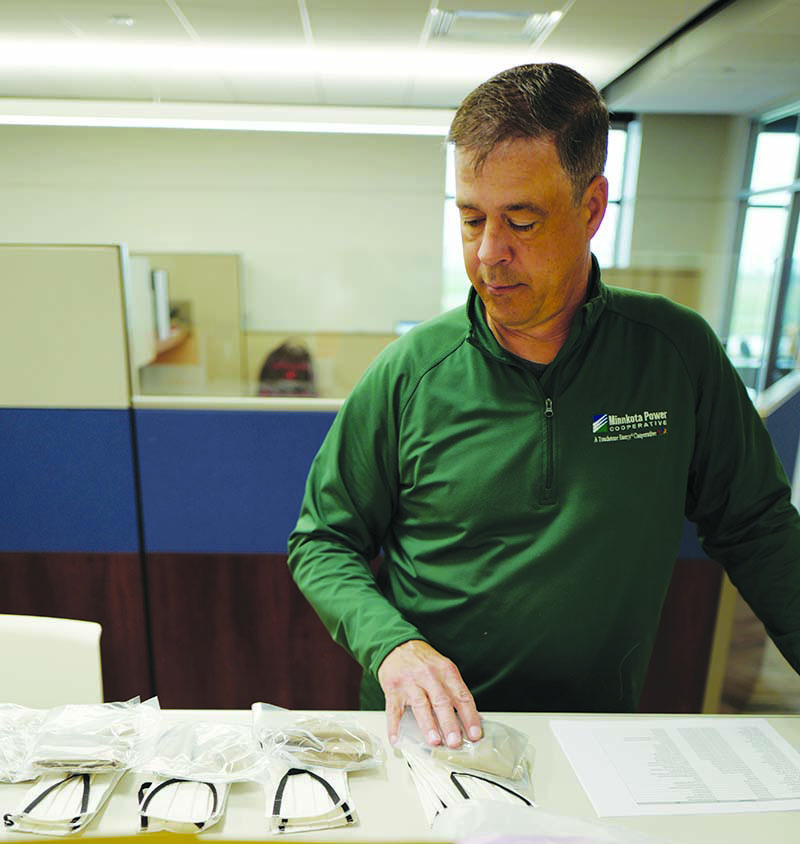
From your living room
For now, the hallways of Minnkota are mostly quiet. Many employees haven’t been in the same room together for months. Bedrooms, living rooms and basements have been turned into temporary offices.
In short order, Minnkota’s Information Technology department distributed additional mobile technologies and enhanced remote working capabilities, all while still protecting the cooperative from cybersecurity threats. Video conferences have become the common way for employees to collaborate. Even Minnkota’s board meeting was conducted online with each director occupying a small square on the digital screen.
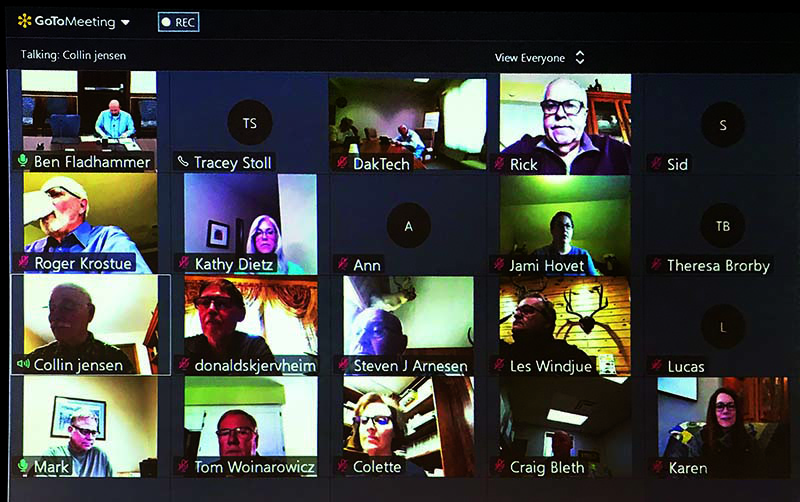
Despite distractions and obstacles, Minnkota’s employees have continued to make progress on important projects and have kept the power flowing safely and reliably into local communities. The camaraderie is still there, too.
“We text and Snapchat together quite a bit,” Tretter said of the power system operator team. “We’re a pretty tight group.”
The pandemic team is evaluating ways to gradually transition employees back to normal operations, but it will be a new normal. Things will be different, but if the past few months are any indication, Minnkota’s employees will respond.
“There’s always the common thread that the North Dakota community does a great job of pulling together and rising to whatever challenges we face,” Uhlir said. “This particular situation forces us to be separated, but we are still seeing that same spirit of community.”
Minnkota response to COVID-19
In mid-March, Minnkota implemented a series of stringent and detailed protocols to manage issues surrounding COVID-19. This multifold response plan included:
- Employees were requested to perform self-monitoring and to not report to work if they were sick.
- Employees who were able to work from home were asked to do so to minimize exposure.
- Facility access to Minnkota’s Grand Forks campus and the Milton R. Young Station was limited to business-essential personnel only.
- Enhanced cleaning and disinfection procedures were implemented, including the use of hospital-grade cleaning products and the installation of employee sanitization stations.
- Power delivery crews, who primarily work outside, were separated into different project areas to allow for greater social distancing.
- Power plant personnel were split into smaller, non-overlapping shifts to limit the number of people on-site at the Milton R. Young Station and to allow for greater social distancing. Lunch breaks and break times were staggered to minimize exposure.
- Employees were required to self-quarantine if they exhibited symptoms of COVID-19, traveled to potential high-risk areas or had close contact with someone who tested positive for the virus.
- All employees were given cloth masks to wear at work and in public.
Main image: Matt Foster, engineer II, is the only employee in a long row of workstations at Minnkota’s Grand Forks headquarters. Many employees are working from home as a precaution against the spread of COVID-19. (Michael Hoeft/Minnkota)
...