Supply chain reaction
Minnkota's Procurement team is finding creative solutions for post-pandemic prices and lead times.
Thain Bouvette is the king of his castle – and his castle is a 28,000-square-foot supply repository on the edge of Grand Forks, N.D. As Minnkota Power Cooperative’s warehouse foreman, every piece of transmission and substation equipment goes through his team before it is deployed in the field. Thousands of widgets and doodads stand waiting for the next lineworker, technician or electrician to load up for a job.
“There’s material moving in and out of here every day,” Bouvette said, surrounded by towering racks of pallets and packages.
The rules of his kingdom have changed a bit since COVID struck in 2020. The worldwide pandemic threw a wrench in the reliable supply chain of goods the industry had come to expect.
“We’ve had to be more resourceful in the sense of, since the pandemic, lead times have gotten incredibly long on material,” Bouvette explained. “There are quite a few items in this warehouse that go out on a job every day, and we’re constantly strapped for it because we’re waiting for it to come in. That has been a challenge.”
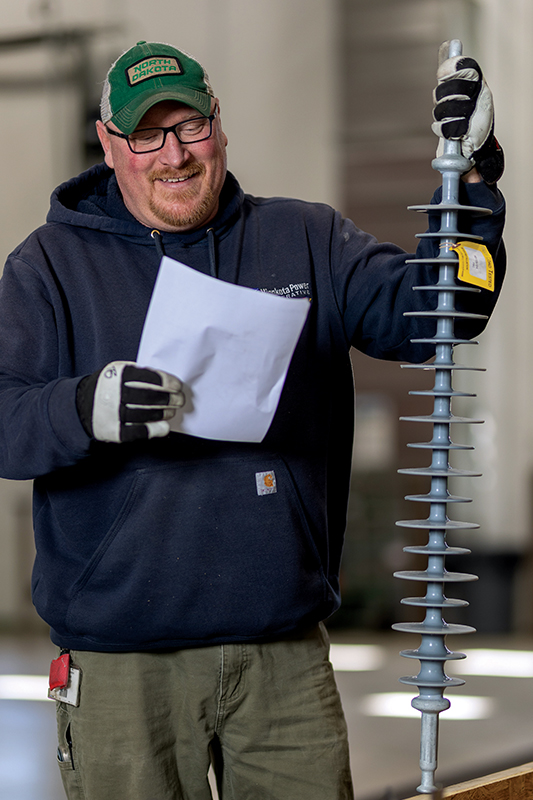
Minnkota isn’t alone in battling a volatile supply chain. Across the nation, organizations are facing higher-than-ever prices on raw materials and supplies and longer-than-average lead times to get them. It began as a problem spurred by a manufacturing workforce sent home during the pandemic, leaving less supply to go around. Now, there just aren’t enough skilled workers to fill those jobs, so materials remain hard to get.
“Costs and leads times both definitely increased, and I feel like there is less room for negotiating now,” said Sadie Gilbraith, Minnkota Procurement Services Supervisor. “In the past, if a supplier said, ‘We can get it in six weeks,’ and we needed it in two, we could make something work. Now, that’s rarely a possibility.”
Minnkota Procurement Manager Scott Schreiner agrees, adding that even the strongest relationships this team has built with vendors over the years can’t overcome new prices and shipping times. “We can’t rely on them to be the backstop for us anymore. We’re in it together, but we now need to do a better job planning ahead,” he said.
In collaboration with the Project Management Office and Engineering, Minnkota’s Procurement department is finding ways to get ahead of lead times that can quickly change. For example, on a Monday, an insulator order may have a lead time of three weeks. By the following Monday, the wait could have stretched to 62 weeks. To make sure they’re on track to get what they need, the departments meet monthly to assess project status, preview future projects and ensure requisitions have been made for those projects – even if they are a year away.
Minnkota’s Grand Forks facility, responsible for the transmission and substation work of the cooperative, approaches ordering in a project-to-project style. The Milton R. Young Station power plant in Center, N.D., has more of an outage-to-outage style. They are used to working a year ahead to acquire dozens (if not hundreds) of items needed for planned maintenance outages. But they’ve still felt the supply pinch post-2020.
“With the Unit 1 major outage planned for this fall, we started working on the turbine package for that at the end of 2023,” Gilbraith said. “It really comes down to time. The more people planning ahead, the better off everybody will be.”
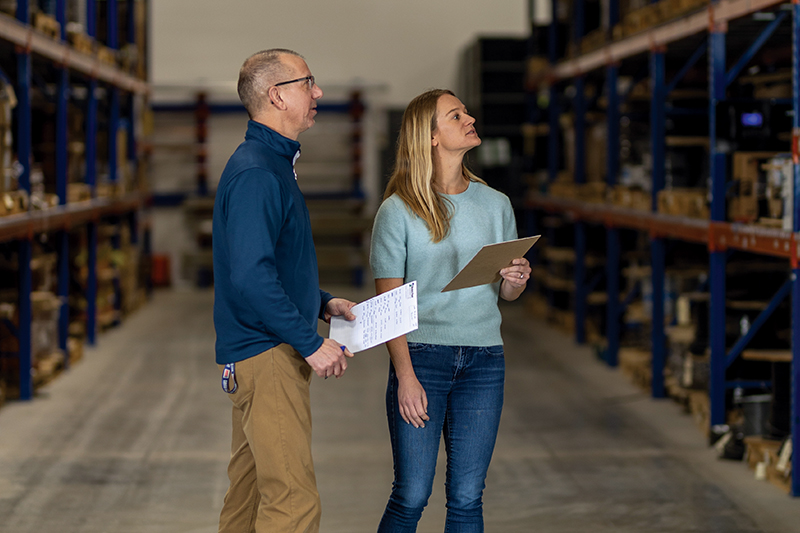
Taking initiative
In 2024, Minnkota’s annual Business Plan includes an initiative focused on evaluating and developing strategies regarding supply chain risk management. Simply stated: Minnkota is raising its supply chain game.
“We actually just kicked off the group that is going to lead that effort to look at a number of things pertaining to our supply chain,” Schreiner said, describing the collaborative process that will take place between his team and co-op leadership. “We’re looking at everything to try to improve Minnkota’s position related to supply chain.”
Three key areas that will be examined in the initiative are supplier and contractor management; physical space utilization and enhanced inventory management practices; and planning and budgeting. Minnkota’s inventory management is already strong in both Grand Forks and Center, but the team is looking into additional bundling and key supplier alliances to reduce long-term costs and ensure supply is there when it’s needed.
Minnkota is preparing for the reality that supply chain challenges will not be letting up any time soon. “It’s going to be quite a while. If at all,” Schreiner said.
Every year, thousands of requisitions come through the Procurement department. The volume of work done by Schreiner and his team is tremendous, and it’s all to support the work being done by other departments across the cooperative. A mountain of teamwork is involved in finding the right items for the job, for the right price, at the right time.
“Minnkota never stops striving to find better ways to keep it all rolling. From engineering all the way down to us in the warehouse,” Bouvette said. “You have to have material. So, if lead times are crazy long, they’re constantly looking for ways they can remedy that.”
MAIN IMAGE: Minnkota Warehouse Foreman Thain Bouvette grabs a capacitor from a rack in the Grand Forks warehouse. (Minnkota/Michael Hoeft)
...