Syncing the sound
From innovative engineering to flawless work in the field, Minnkota is working to enhance and improve its demand response system.
There are soundwaves hidden beneath the gentle hum of Minnkota’s power delivery system that engineers and technicians work tirelessly to perfect. They turn dials, tweak settings and monitor signals pulsing through the cooperative’s ripple injectors in hopes of finding a perfect harmony.
There was a lot of buzz in 2020 around Minnkota’s ripple injection system – the unique set of equipment that drives the cooperative’s demand response program. Two ripple injectors were replaced with new equipment, custom communication technologies were deployed and a full-system sync was performed for the first time in nearly 50 years of operation. This work will inform one of the most thorough review and modeling efforts on all 17 ripple injectors in the Minnkota system.
“This is our first time really looking at the entire system, not just making fixes at one or two sites,” said Kasey Borboa, electrical engineering supervisor. “If you can imagine throwing 17 soundwaves all together and trying to line them up at different distances, that is exactly what we’re doing.”
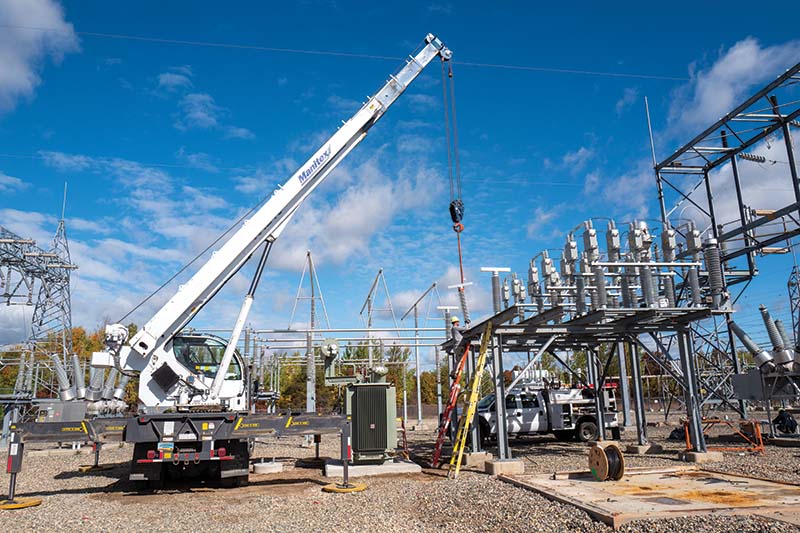
Ripple injectors send tens of thousands of electronic signals throughout the entire transmission system and into the distribution system. Receivers plugged into standard electrical current at homes and businesses can read the signals, and when the appropriate message is sent, the receivers interrupt the electric power flowing to an electric heating system, water heater or other controllable load. When control is no longer needed, a signal is sent to turn the electric system back on.
All injectors need to work together and fire at approximately the same time to ensure the signal reaches across the entire 35,000-square-mile system served by Minnkota and the membership. The process of tuning and syncing the injectors is a combination of art and science.
“Tuning an injector is like tightening the strings of a musical instrument to make sure it vibrates at a certain frequency,” said Nick Gellerman, Minnkota’s lead engineer on the project. “Syncing all the injectors together is like coordinating an orchestra and making sure that your violins, drums and other instruments are all playing at the same time.”
With the entire system off, crews started syncing all the larger injectors, which have the strongest signal strength. As adjustments were made, Gellerman monitored the results on his laptop.
“It requires a very fine timing adjustment,” Gellerman said. “We adjust things by about a millisecond at a time until we get to the highest signal possible.”
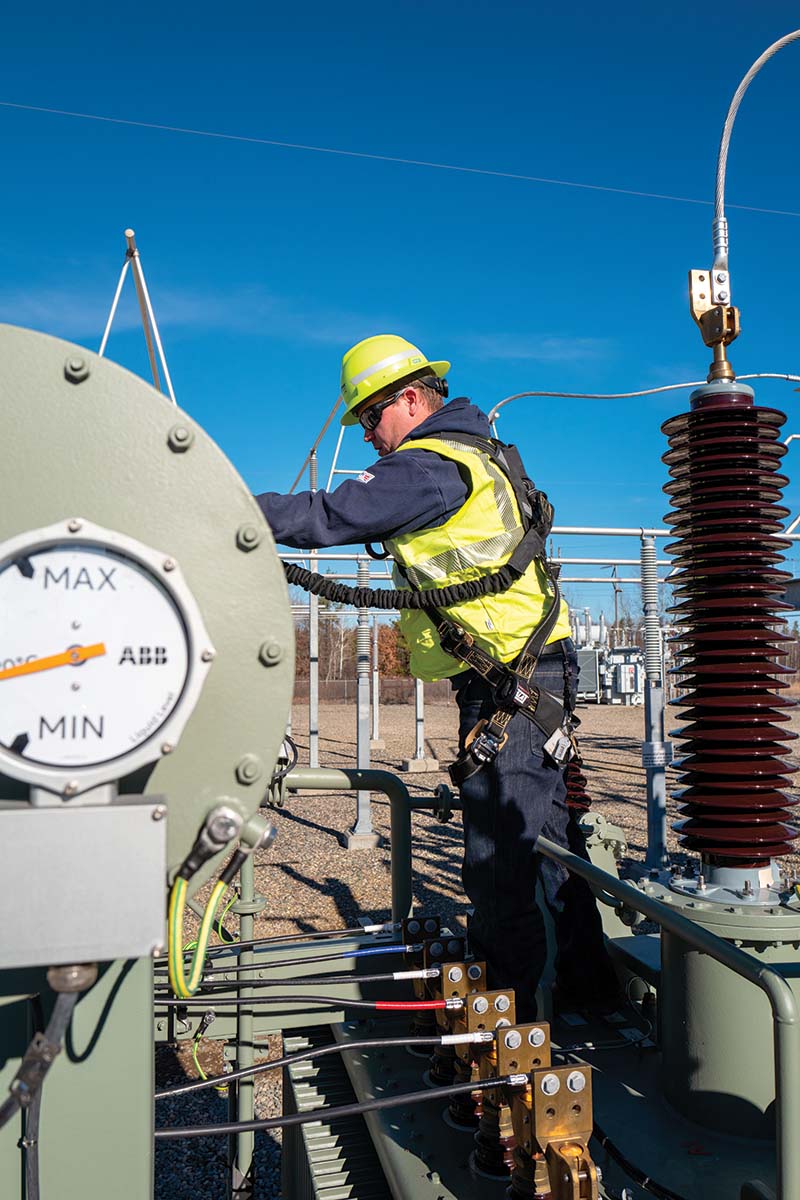
Two-way communication
Minnkota became a pioneer of demand response in the early 1970s when the ripple injection system was built. Since then, the program has become one of the most successful and unique in the country with more than 55,000 consumers participating. By reducing the demand for electricity during peak usage times, Minnkota is able to avoid purchasing costly excess power from the wholesale market, which saves money for the membership.
While many utilities use radio or Wi-Fi to send their demand response signals, Minnkota has committed to the ripple injection system because the infrastructure is in place and it has proven to be highly reliable through harsh winters and sweltering summers. Historically, the challenge has been that the system was only designed to provide one-way communication.
Borboa said that countless vendors were asked to develop a device that would provide additional data and two-way communication. There were few takers, and those who were interested required a substantial research and development investment from Minnkota with no guarantees of success. Instead, Borboa decided to ask Gellerman if he could design a solution.
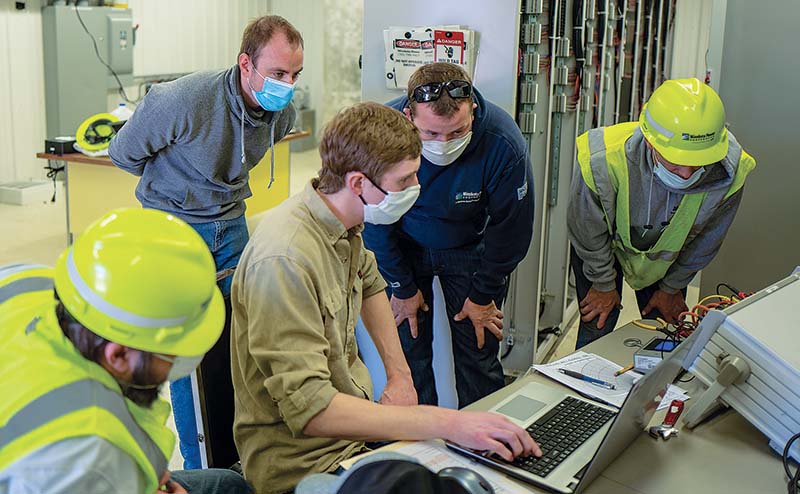
Although there was no instruction manual or template to follow, Gellerman delivered the ripple monitor device, which is fondly referred to as the “Geller-meter” in some circles at the cooperative. The equipment measures the system’s signal strength and communicates that data back to the cooperative’s control center.
Information gathered from the ripple monitors is being used to develop a demand response system model that will help identify signal issues and determine the potential effects of a transmission line failure or ripple injector malfunction. It will also determine if ripple injectors need to be moved to different substations or if new equipment should be purchased.
“Now we know what the signal is doing at the end of the line and what the consumers are likely seeing,” Borboa said. “We have a much better sense of how different outages effect certain signal levels and when system changes are occurring.”
“It’s been a pretty fun project,” Gellerman said. “It’s unlike any of the other projects we do around here.”
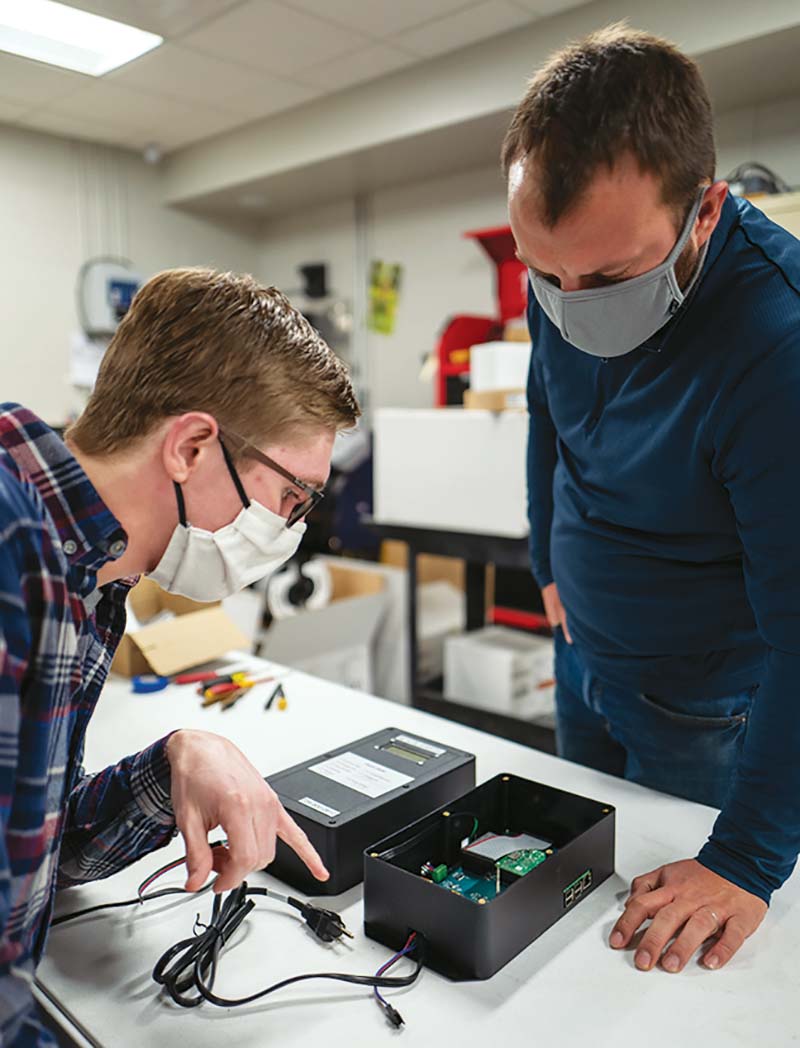
Minnkota technicians have installed ripple monitors at 50 substation sites and, over the next few years, plans are to have the devices at nearly all 255 substations. Having consistent data from the field will help ensure the system is performing reliably.
“The ripple monitors help us tremendously,” said Jason Bjerke, senior technical maintenance technician, who has worked on building and installing the devices. “Now we know what is happening across the system. If the co-ops are seeing issues, we can call that ripple monitor and find out what’s going on.”
Legacy system
Over the last five years, Minnkota has replaced 10 of the 17 injectors with new equipment, including the West Fargo 69-kV injector and the Wilton (Minn.) 115-kV injector in 2020. Plans are to have all injectors replaced by the end of 2024.
With little access to vendors or experts in the United States, Minnkota purchased the injectors from a Swiss company and works with Solutec’s Patrick Rickenbacher. Even in a pandemic, Rickenbacher’s critical infrastructure worker designation allowed him to travel from Switzerland to the United States and, after following proper quarantine and self-monitoring requirements, help with the new injector installation at Wilton substation this fall.
Rickenbacher said the uniqueness of Minnkota’s system provides a learning experience for him as well.
“I’m impressed with the size of this system,” Rickenbacher said. “In Europe, you have a city that has its own ripple control system. The radius is about 10 miles at most. This system is much different and the injection level is much higher, but that makes it more interesting to work on.”
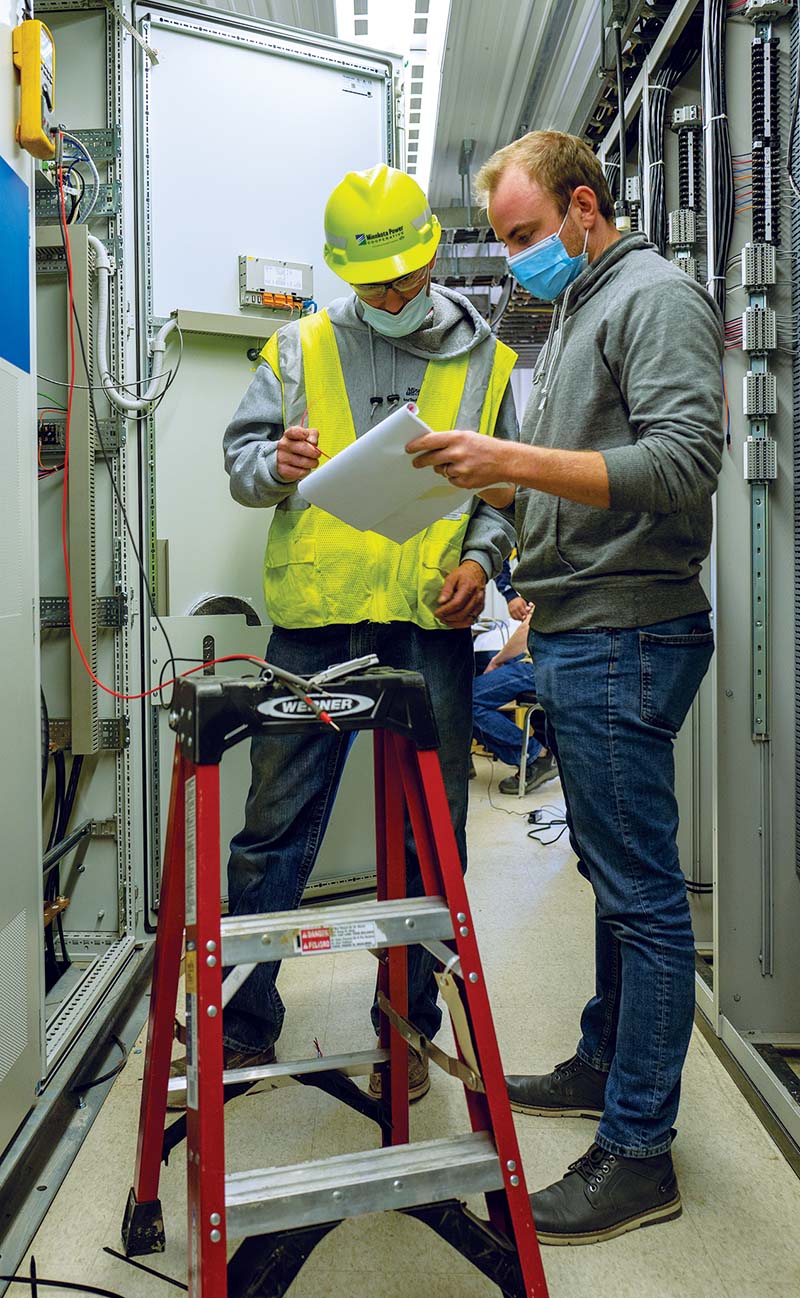
Rickenbacher has traveled to the United States five times to work with Minnkota. During those trips, work connections have turned to friendships.
“We work together very closely,” Rickenbacher said of Minnkota’s employees. “They’re not just giving me the keys and leaning back in their chairs. They want to know how things work. You can tell they really care about the system.”
Main image: Surrounded by the northern Minnesota woods, Jason Bjerke, senior technical maintenance technician, adjusts ripple injection equipment at the Wilton substation. (Minnkota/Michael Hoeft)
...