All in for the outage
Milton R. Young Station leaders leverage team coordination and adaptability for safe and successful planned outages.
A major outage at the Milton R. Young Station is no game.
But to successfully complete one, the unit in charge of planning the six-week undertaking has to pull out the skills valuable in the best tabletop pastimes – strategy, adaptability and patience.
“I have 200 chess pieces. I have to decide, where are they going today?” said Paul Goldmann, Minnkota’s senior maintenance coordinator for the past three major outages at the Young Station.
There’s no rolling the dice on coordinating the massive interdepartmental effort, so Goldmann works with his teammates, plant managers Andrew Freidt and Tim Hagerott, to create a framework.
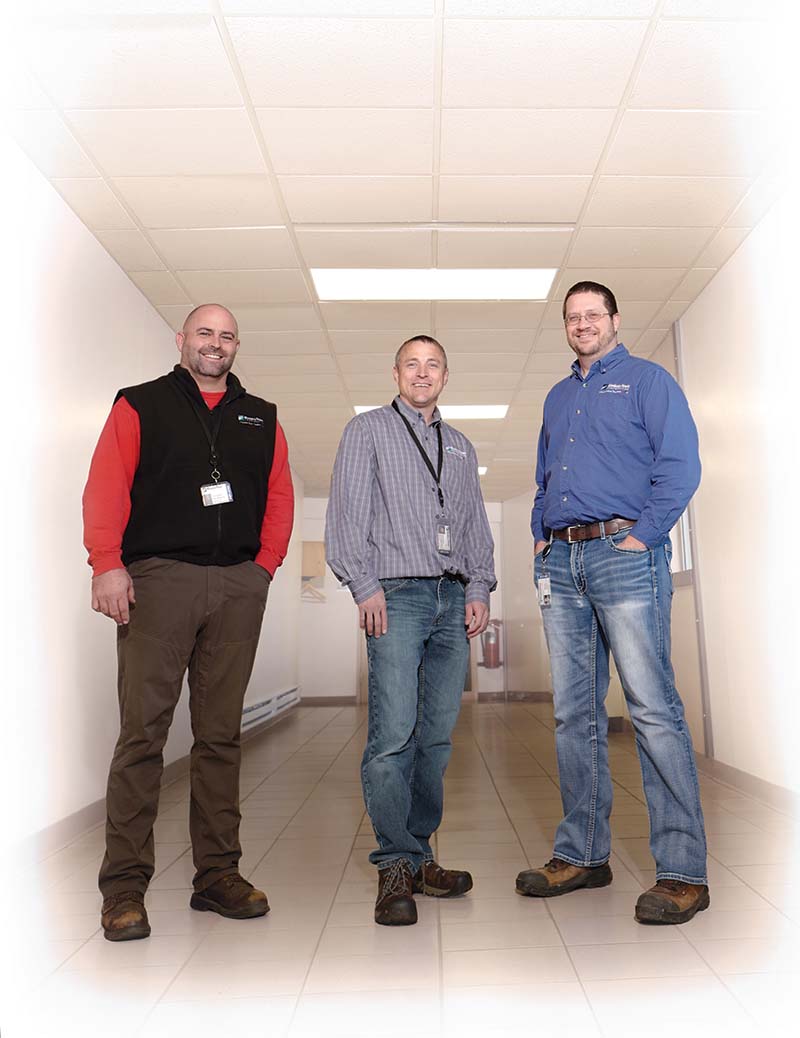
“It’s a 10,000-piece jigsaw puzzle. It would be nice if it was just the six-piece jigsaw puzzle, where the pieces are really big,” Hagerott explained, his metaphor provoking smiles and nods from the others. “But it’s like the really small ones where, if you lose one, you can’t find it on the floor. It’s a lot of moving parts.”
The Young Station’s most recent major Unit 2 outage started in early September 2019 and wrapped at the end of October. The Minnkota crew worked alongside up to 470 contractors to complete inspections and maintenance in major areas such as the boiler and turbine, as well as projects like replacing expansion joints, improving valve performance and overhauling the primary coal crushers.
Although the outage itself lasted less than two months, the game plan started forming years in advance.
“Physical work is one thing. If you look from a planning perspective, that started back, in some regards, in 2016 as soon as we finished the last major outage,” Hagerott said. “It’s a big process. The actual outage window period is really the culmination of the planning and work that goes into it on the front end.”
Coordinating the chaos
Once outage projects were selected and budgeted at the end of 2018, Goldmann and his team of a half dozen maintenance coordinators started meeting with engineers, plant specialists and department leaders. The small groups met several times until everyone had a solid understanding of what the respective projects would entail. Then, groups started combining for bigger-picture conversations.
With just six weeks to work with, every small planning choice could impact others and the larger goals of the outage. Communication was essential.
“In many cases you can’t have multiple jobs working in one area at the same time, so you have to juggle that,” Goldmann said. “You might schedule things on day shift or on night shift so that we can get it all done in a six-week timeframe.”
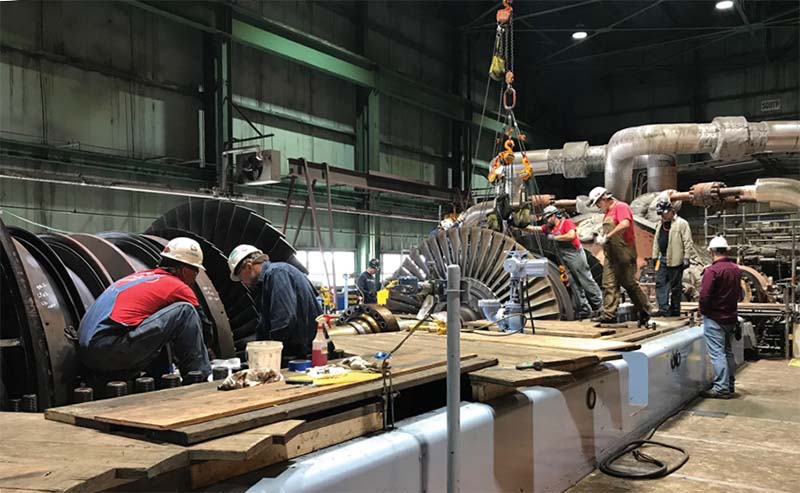
Scheduling only Minnkota manpower is hard enough. But Goldmann and his project managers also had to balance the resources of more than 60 contracted entities, many with dozens of people on their crews. These contractors often fly in from other states, so it was critical to get the timing right.
Many of the contractors have worked on Minnkota outages for years and have developed a strong understanding of the plant and the people in it.
“It’s really easy working with them. They know our plant better than some of our newer guys know our plant and they’re helping guide our people in becoming more efficient,” Goldmann said. “We’ve been building these relationships for years.”
“It’s not an adoption to the team – they are a significant part of our team,” Freidt added.
Safety through adversity
Even the best-laid blueprints find themselves monkey-wrenched in a major outage. Because a bulk of the work is inspection-based, the crew doesn’t know what they’ll find until the equipment is opened up.
The latest major outage brought an onslaught of adversity like a high volume of ash buildup in the boiler, two concurrent forced Unit 1 outages and a pesky early blizzard that kept some out-of-state contractors from driving to the plant.
“You come in in the morning and by 7 a.m. you’re like, ‘Well, this is not what I wanted to do today,’” Hagerott said. “You get really good at managing where all the people are. When we run into an issue, we can we move people around to be most efficient. It’s like that every day. You constantly adapt.”
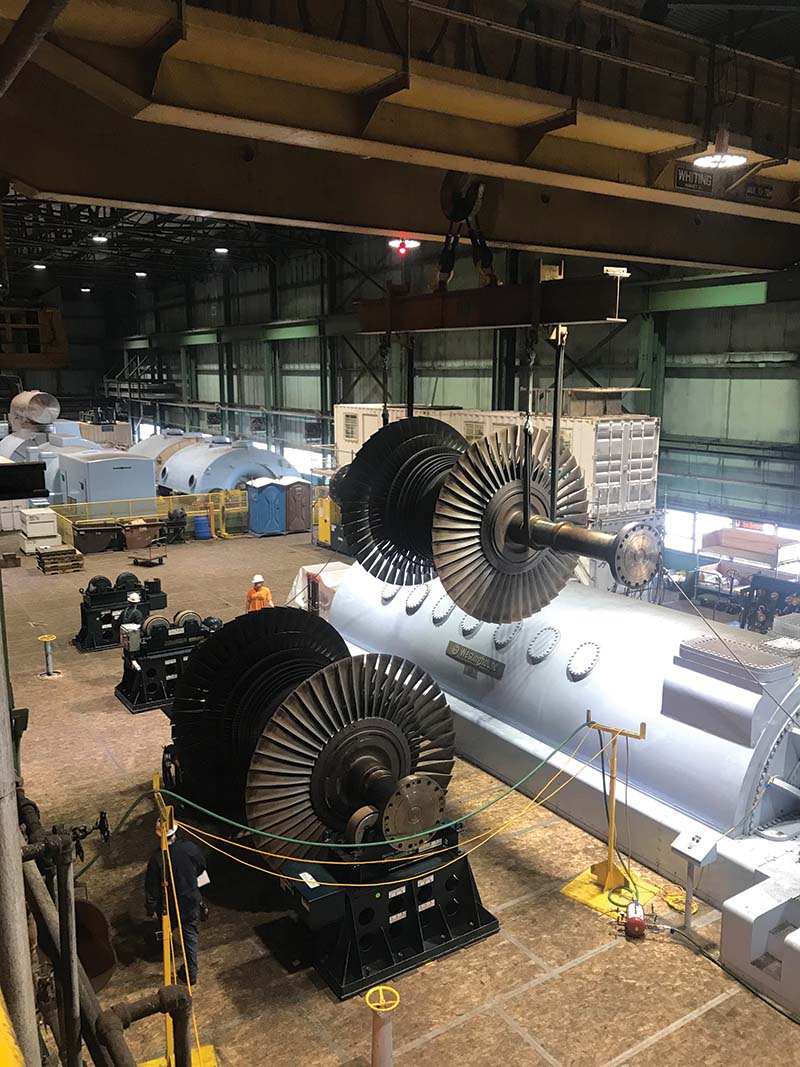
A lot of rerouting happens on the fly, but the team always takes it slow enough to avoid missteps.
“Safety is huge,” Goldmann emphasized. “It’s always the number one thing that we stress.”
In April 2019, the Young Station passed a milestone of 1 million work hours without a lost-time injury. The outage wouldn’t stand in the way of continuing that streak. The focus on safety involved prejob briefings to understand the hazards of the work, daily JSAs (job safety analyses) and the incorporation of contractor safety representatives who met weekly with Minnkota’s safety staff to discuss the projects ahead.
“The key is planning. Paul [Goldmann] always says, ‘The more we can plan these jobs, the safer they are,’” Freidt said.
Not over ’til it’s over
When the outage ended and the plant was firing again, the work wasn’t done. Coordinators and project managers jumped straight into postoutage reports and assessments that allow them to learn from the experience and start prioritizing discovered needs for the next major outage.
As sometimes happens, the endeavor ran a few days past schedule. However, with the main goals accomplished and a sterling safety record intact, Goldmann considers this another success for the plant.
“From the hand we were dealt at the beginning of the outage, and how we adjusted to the early complications, I think we did a very good job getting to the end,” he said.
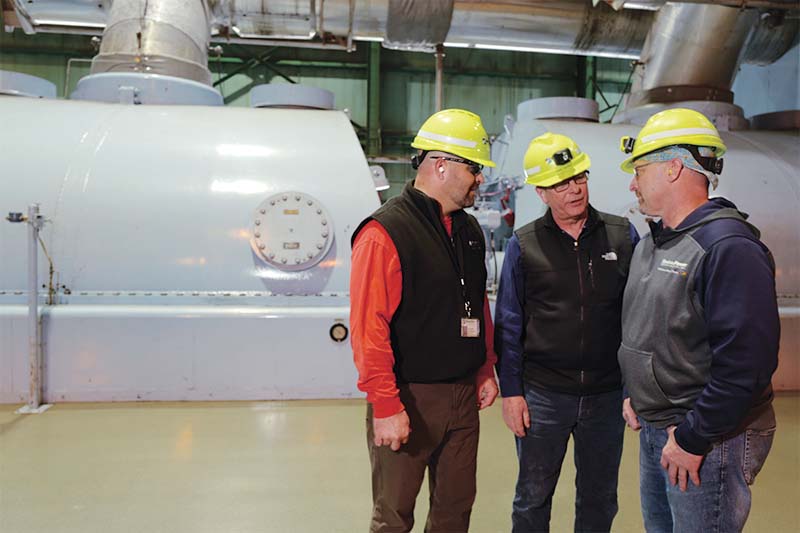
The challenges and time crunches have bonded Goldmann and his outage entourage. He recalls banter with his coordinators, late night calls and texts with Freidt and Hagerott, and a celebratory pizza party and sloppy joe feed with the contractors and crew.
Executing an outage is no game – but that doesn’t mean it can’t be enjoyable.
“It’s fun,” Goldmann grinned. “I get to work with some good guys who make my job easier.”
...