‘Keep calm and outage on’
Milton R. Young Station employees have once again used a major planned outage to keep Unit 1 strong and reliable.
As other parts of the country have faced grid challenges this year, Minnkota’s membership has avoided major issues due in large part to the reliable operation of the Milton R. Young Station. Whether temperatures are 100 degrees or 30-below-zero, the coal-based facility has responded with stable and dependable energy to keep communities energized and member-consumers protected from volatile energy market pricing.
Leaders at the Young Station recognize resiliency doesn’t happen by chance. Major maintenance outages are scheduled every three years during the fall (when energy demand is typically lower) to complete important projects, conduct inspections and repair equipment. In 2021, it was Unit 1’s turn to undergo a major scheduled outage. The 250-megawatt generator came offline Sept. 8 and was successfully returned to service on Oct. 26.
The outage was completed on schedule and on budget with no major safety issues. About $6 million in capital projects were completed, along with about $12.3 million in operating and maintenance efforts.
“The units were built with the idea that they could be reliable for a very long time,” said Andy Freidt, plant manager of operations and maintenance. “With the right strategies we can ensure that happens. The major outage is our time to do as much as we can possibly can to achieve our availability goals for the next three years.”
For Unit 1, that goal is 93% availability in non-major outage years. The unit has met this target in each of the last four applicable years – even as it nears its 51st year of operation.
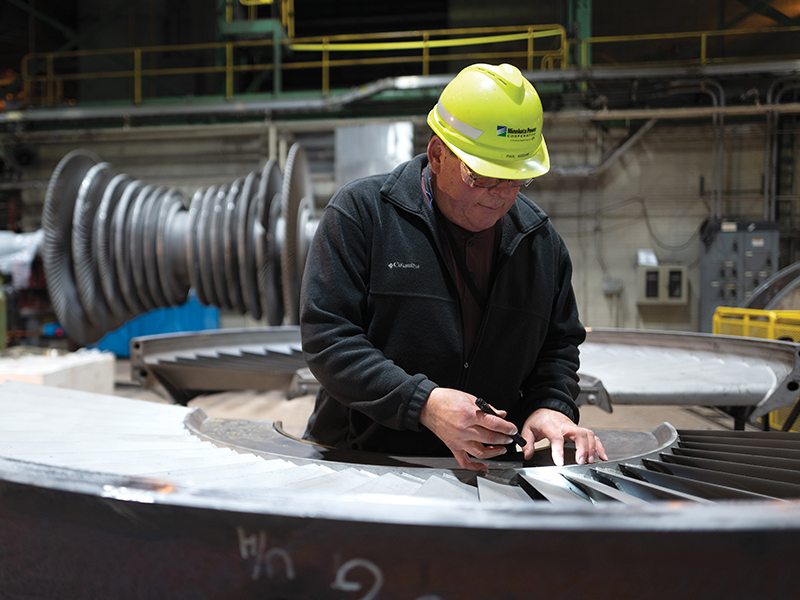
Although the reliability of the unit has been consistent, operating practices have changed in recent years in response to the dramatic price swings experienced in the energy market. More than ever before, both Young Station units are asked to increase or, more typically, decrease their net output based on system demands and economic indicators.
“This will be the first major outage we’ve taken since these alternate operating strategies have been used significantly,” Freidt said. “We’ll take this opportunity to conduct detailed inspections on how these different modes of operation impact our maintenance needs.”
Finding solutions
Minnkota staff spend months preparing for major maintenance outages, each of which presents its own set of unique challenges and opportunities. Hundreds of specialized contractors are onsite, millions of dollars in projects need to be managed and countless hours of work must be completed safely and efficiently.
“Our message was ‘Keep calm and outage on,’” said Tim Hagerott, plant manager of engineering and environmental. “There’s a lot of our staff who hadn’t been through a major outage before, so this was a learning experience for a lot of people at the plant. We know that things will change as we get into projects, and we just have to roll with it, adapt and find solutions.”
Adding in a global pandemic and a tightening market for materials put pressure on staff leading up to this year’s outage. COVID safeguards, including mask requirements, socially distanced break areas and other sanitization practices were implemented to help provide a safe and healthy work environment. The days of squeezing large groups into conference center rooms for project briefings were replaced by meetings spread out across large vehicle storage buildings. Scheduling changes were also implemented in an effort to limit the amount of overtime needed for the outage.
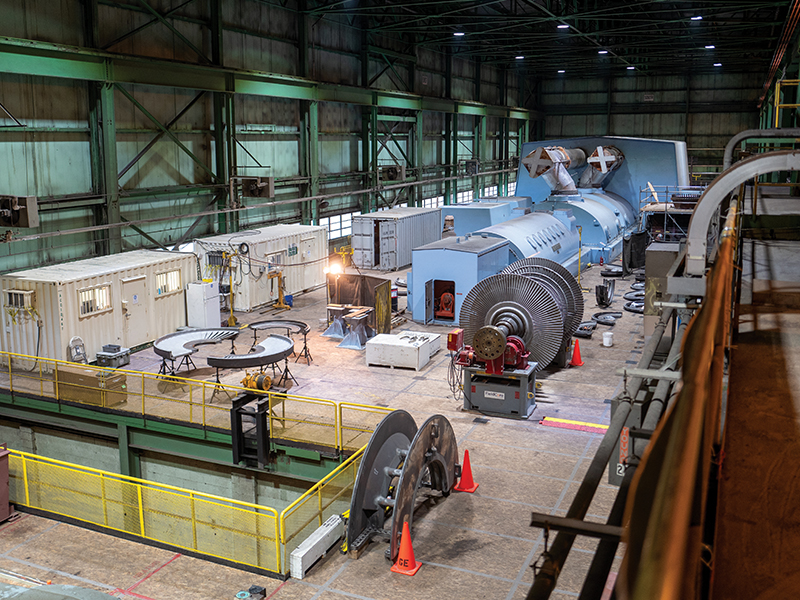
Project plans were developed earlier than normal to ensure equipment and material could be obtained. The Young Station expanded its material inventory in anticipation of the outage and the potential for finding “discoverable work” – those unforeseen repairs or projects beyond the original scope of the outage. In most cases, these issues cannot be identified until the unit is fully shut down and inspected.
“You’re seeing it across the board – things are just taking longer,” Hagerott said. “We emphasized that early on, so we could get out ahead of our material needs.”
Looking ahead
When the Unit 1 outage wrapped up this fall, there was no time to rest for the Young Station staff. A three-month major outage is scheduled for Unit 2 in the fall of 2022, which will require planning efforts to ramp up this winter.
Prudent maintenance and project work has helped Unit 2 exceed 93% availability in recent non-major outage years. Through October 2021, the plant currently is at a 92.6% availability rating.
Lessons learned from the Unit 1 outage will play an important role in how the Young Station staff approach future outages. The goal is to make sure both units are ready for the next polar vortex or heat wave – when the demand for energy can skyrocket.
“It’s an evolving process,” Hagerott said. “We’re always completing as much inspection work as we can and determining which projects provide the most overall value to our future operations.”
MAIN IMAGE: Koedam uses a flashlight to inspect the Unit 1 turbine blades. (Minnkota/Michael Hoeft)
...