Major outage insight
Minnkota’s Young Station team has successfully navigated another lengthy maintenance outage with planning and teamwork.
Minnkota engineer Sam Schwanberg and plant specialist Roger Bauman turned into a bit of a dynamic duo over the last quarter of 2022. They were in the midst of tackling projects only possible while the Young Station’s Unit 2 was offline, and they needed each other’s help to do it.
The planned maintenance outage of Unit 2 was just the second major outage Schwanberg had experienced since joining the Minnkota team full-time in 2020. For Bauman, who was hired at Minnkota nearly 37 years ago (before Schwanberg was even born) the experiences are harder to count.
“I have no idea how many major outages that’s been. No idea,” Bauman said with a laugh. “But I can guess how many I have left.”
Schwanberg was quick to reply. “He jokes about retirement, but we won’t let him leave,” he teased.
This pair was two of hundreds of Minnkota employees and contractors working together through a unique 13-week to-do list of cleaning, inspecting and refurbishing many components of the power plant’s second unit.
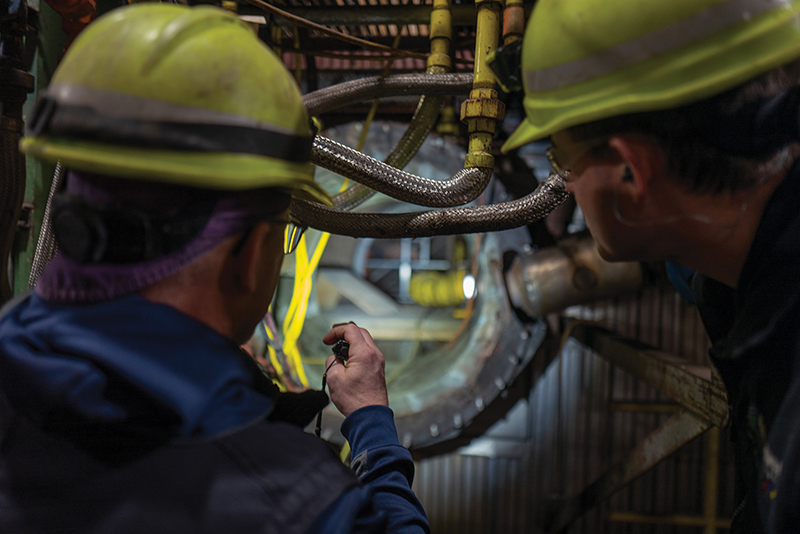
“Once every three years you get to look at the internals. You get to look at the guts,” said Wayne Haag, plant manager of Engineering and Environmental. Haag described the intricate process of powering down the unit and then examining and fortifying every nook, from the water intakes all the way to the back chimneys. It’s a load of work, and it takes a load of brains and brawn to pull it off every three years.
“It’s an unbelievable number of people,” he said of the average 130 employees and 250 contractors that passed through the Young Station daily. “It almost turns into a small city out here when you get going.”
Constant communication and care
Of the 50-plus projects planned during the Unit 2 outage, Schwanberg held engineering leadership over a couple of the largest ones. While Bauman’s projects weren’t as enormous, they were certainly more numerous, and had to be executed in the same timeframe and same portion of the plant – the Unit 2 boiler. Communication and coordination were critical to ensure safety and efficiency.
“One of the things that I’ve learned over the years is that whatever you do affects someone else, somehow, in ways you can’t even imagine,” Bauman said. “Over time, I’ve figured out a lot of these – I call them interferences. So Sam and I work together. We’ve worked through a lot.”
“And we still are,” Schwanberg said. “Constantly.”
However, Bauman and Schwanberg’s projects were only a part of the outage as a whole. A team of maintenance coordinators and project leaders must collaborate on a full outage plan to make sure work space, materials, and resources are always available when needed. When one aspect of a project plan shifts, it could quickly create an impact ripple effect.
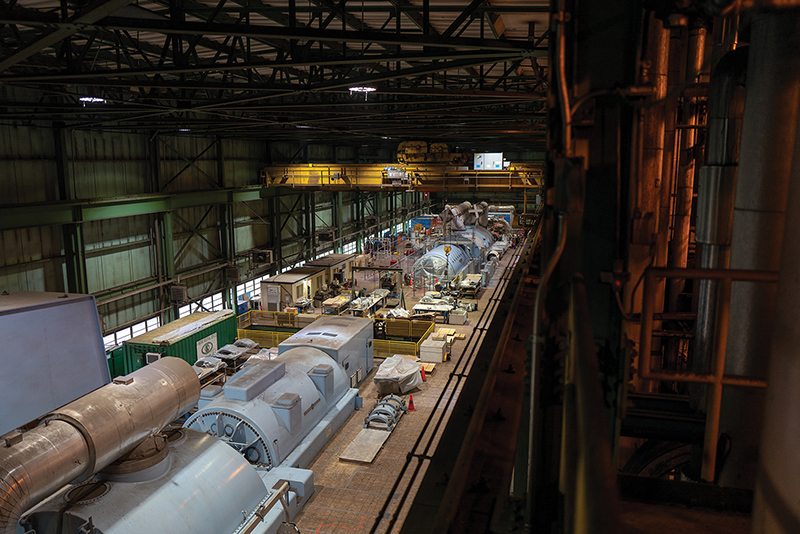
“For example, someone has to sit down and say, ‘OK, you have the vacuum truck from here to here, and this team has the vacuum truck from here to here,’” Haag said, pantomiming stretches of time. “If those times overlap, you’ll need another vacuum truck. Small things like that, like just having a vacuum truck unavailable, can completely stop jobs.”
The coordinators of the latest Unit 2 outage had additional concerns to balance. The material shortages experienced by nearly every industry over the past two years made it a challenge to get key parts and equipment to the plant quickly, made all the more frustrating when unplanned maintenance work was discovered during inspections. And woven through all projects was the common thread of safety, a priority on which Minnkota doesn’t compromise. Contractors are always given a safety orientation at the start of outage work, and job safety plans are discussed for every project with contractor safety personnel.
“Our safety department is constantly out and about. They’re always looking for potential hazards,” Haag said. “Safety is on everybody’s mind.”
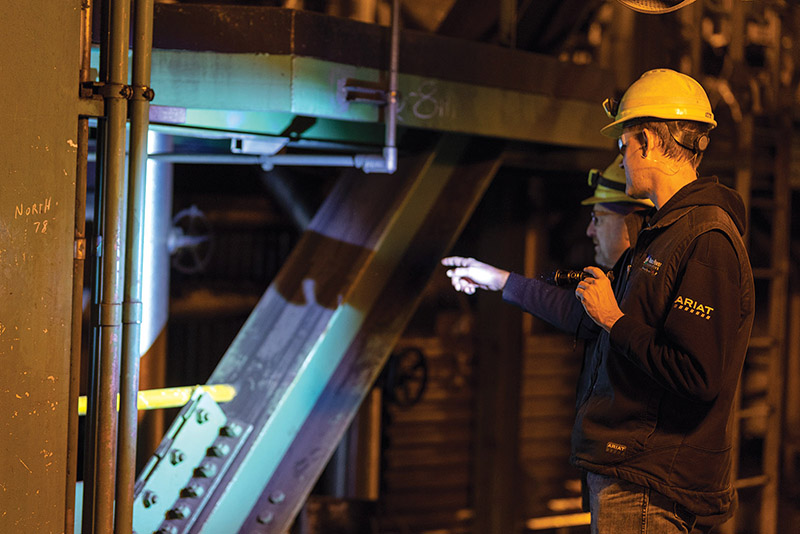
Passing the outage torch
In Haag’s 16 years with Minnkota he has never seen a 13-week outage, which has allowed work to be performed at an easier pace (none of the around-the-clock work of a typical 6-week outage). But this outage was distinctive in another regard. The Young Station engineering team is young. With many veterans retiring over the past few years, the average years of experience on the team is only four.
“We have very few seasoned employees left. We have very few Rogers,” Haag said. “The learning curve is very steep for the newer employees. They often don’t get the advantage that I had when I started here to have a seasoned employee to learn from.”
That’s where the “very few Rogers” come in, working side-by-side with the “Sams” to pass along the years of knowledge they’ve gained in the throes of countless planned outages.
“He’s taught me a thing or two, I’d say,” Schwanberg said, grinning at Bauman. “I go down to his office for one simple, little question, and I end up being down there for two hours with one thing leading to another. When I leave, I’m like … that’s a lot to digest. Roger is super knowledgeable.”
“We have lots of new people, but our engineers are young, bright kids and they learn very fast,” Bauman said. “They’re doing great.”
“I’ve taught him a thing or two also,” Schwanberg continued, referring to a two-way street of knowledge transfer. “His street’s a little longer and wider, but I try my hardest.”
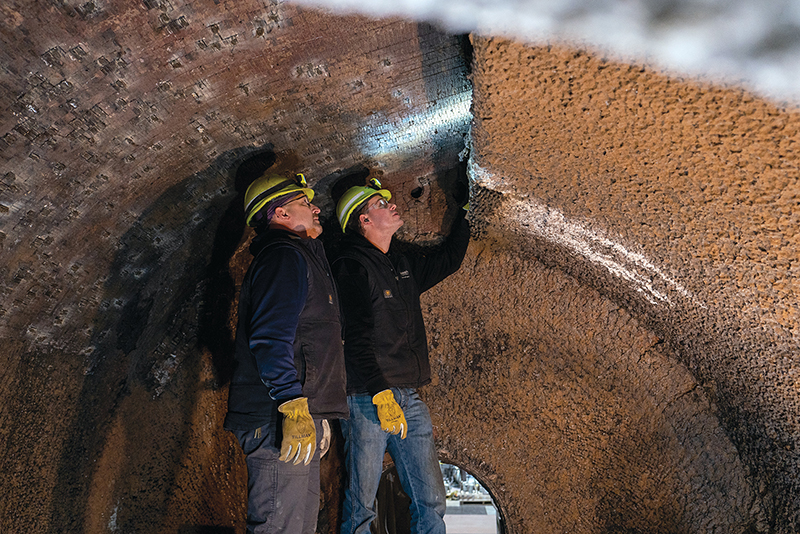
Through all of the collaborative checklists, sweat-drenched huddles, and shared victories of major outages, the Young Station team becomes smarter with the completion of each one. Both units of the plant continue to perform remarkably well after nearly half a century of producing power, and their reliability will persist due to the hard work and commitment of every Sam and Roger.
“It’s obvious that the employees here take pride in this place,” Haag said. “They want to see that it continues putting out safe, reliable, affordable electricity for many more years to come.”
MAIN IMAGE: Bauman (left) and Schwanberg stand inside the Unit 2 boiler, something that can only be done when the unit is taken offline. (Minnkota/Michael Hoeft)
...