Substation communication revolution
Minnkota's system-wide deployment of distribution automation technology is rapidly enhancing response and reliability.
On April 16, several teams assembled at the Grand Forks site of Berg substation, the newest to be integrated into Minnkota’s system of more than 255 transmission and distribution substations across North Dakota and Minnesota. After months of planning and construction, it was time to bring life to the lines and metal.
Energizing day meant lineworkers were removing protective grounds, electrical crews were making sure switches were closing properly and technicians and engineers were double-checking ratings and relays. Power delivery substation engineer Kara Laframboise examined screens alongside technical maintenance pros, completing the long checklist of elements that needed to come together to safely and flawlessly energize the sub.
The anticipation? Electrifying.
“Everybody wants it to be perfect,” Laframboise said as the team performed final phasing tests.
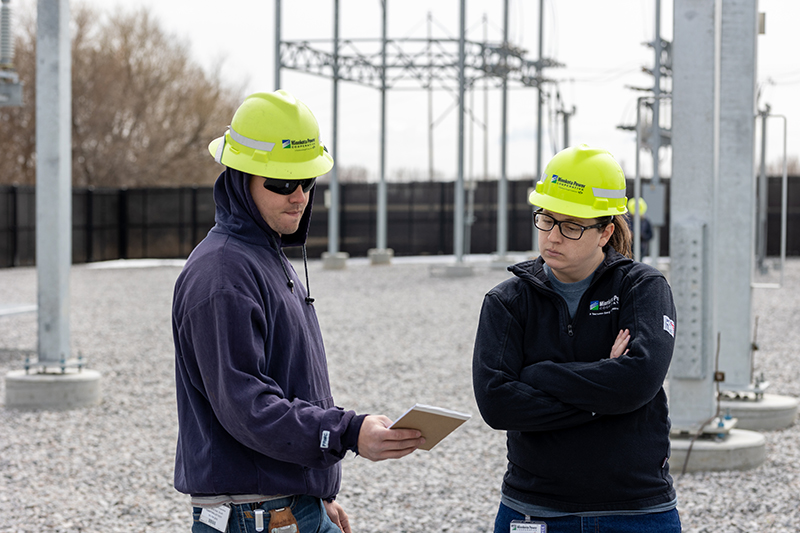
When power began to flow at the speed of light through Berg substation that day, it became the next link in a Minnkota grid that rapidly has become more connected, intelligent and reliable – due in large part to the deployment of distribution automation (DA) technologies.
“The sub design has progressed over the years. It used to be very simplified,” Laframboise said. “But we’ve discovered, as time goes on, that it wasn’t the best design for Minnkota to potentially expand in the future or for maintenance issues.”
Although new subs are now automatically designed with DA equipment, Minnkota is in the midst of a nearly 10-year plan to add the technology to every one of its 215 distribution substations, many of which haven’t had intensive upgrades in decades.
“Before distribution automation, a distribution sub was just a triangle on the power system operator’s board,” explained Dustin Marquis, technical maintenance supervisor and DA program lead. “They didn’t have any information coming back at all. They didn’t even know if it was energized. Now, with DA installed, those in the control center know what the voltage is at the substation, they know the status of some of the transformers and the regulators – all of the equipment in the substation, they can see it live.”
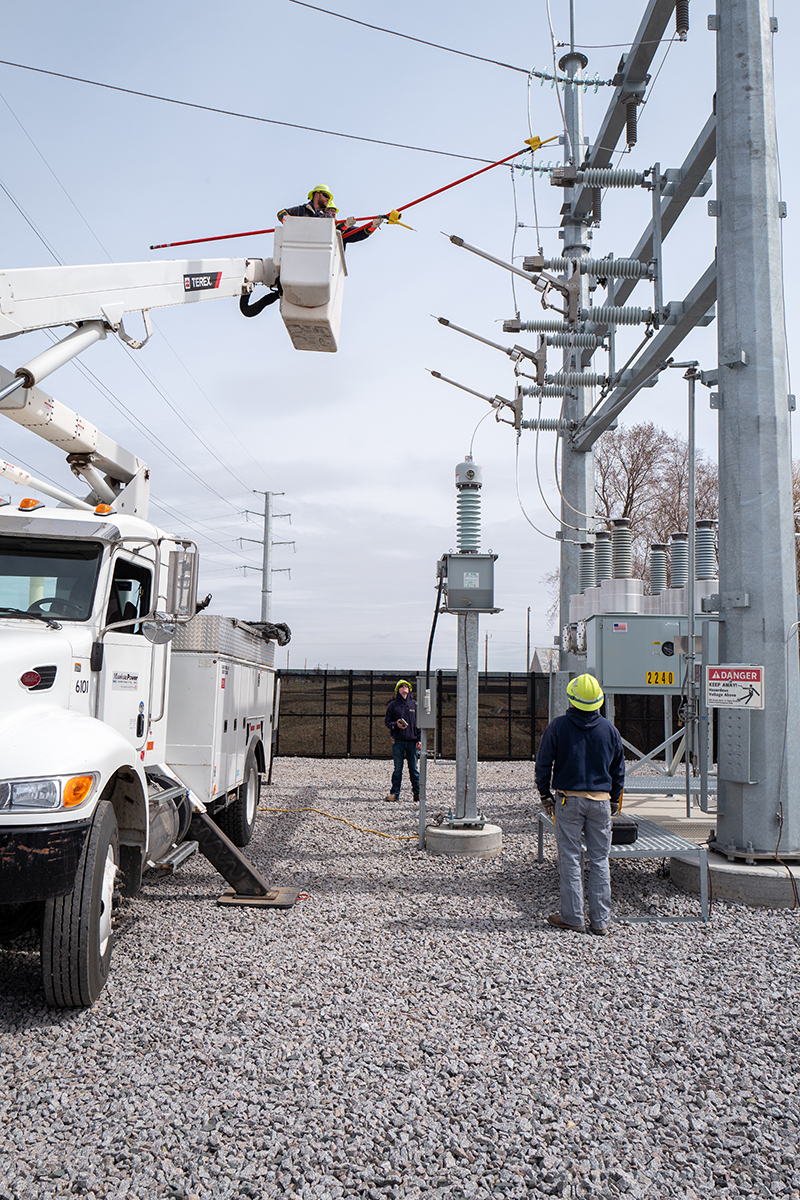
Since the start of the DA initiative in 2018, the technical maintenance crew has partnered with the electrical and telecommunications teams to install the equipment at more than 45 distribution sub sites. They plan to continue retrofitting roughly 15 sites a year for the next few years until all subs are equipped.
A week after Berg substation was energized, a couple of technical maintenance technicians were a few miles away at the nearby Coleman substation, putting the final touches on new DA-ready meter and regulator control panels. The electricians had already completed the prewiring and cabling, the telecomm group had confirmed the sub and control center were communicating, and now it was time for the “painters and carpet layers” to wrap up the project.
“These regulate the voltage at the customer level, keeping it within a certain bandwidth,” Marquis said, pointing to three panels before him. “Before, it regulated the voltage, and that’s it. Now, it regulates the voltage, sends in that voltage to our dispatch, and dispatch can raise or lower the voltage from System Operations. Before all they could do was…nothing. They would have to send someone out here.”
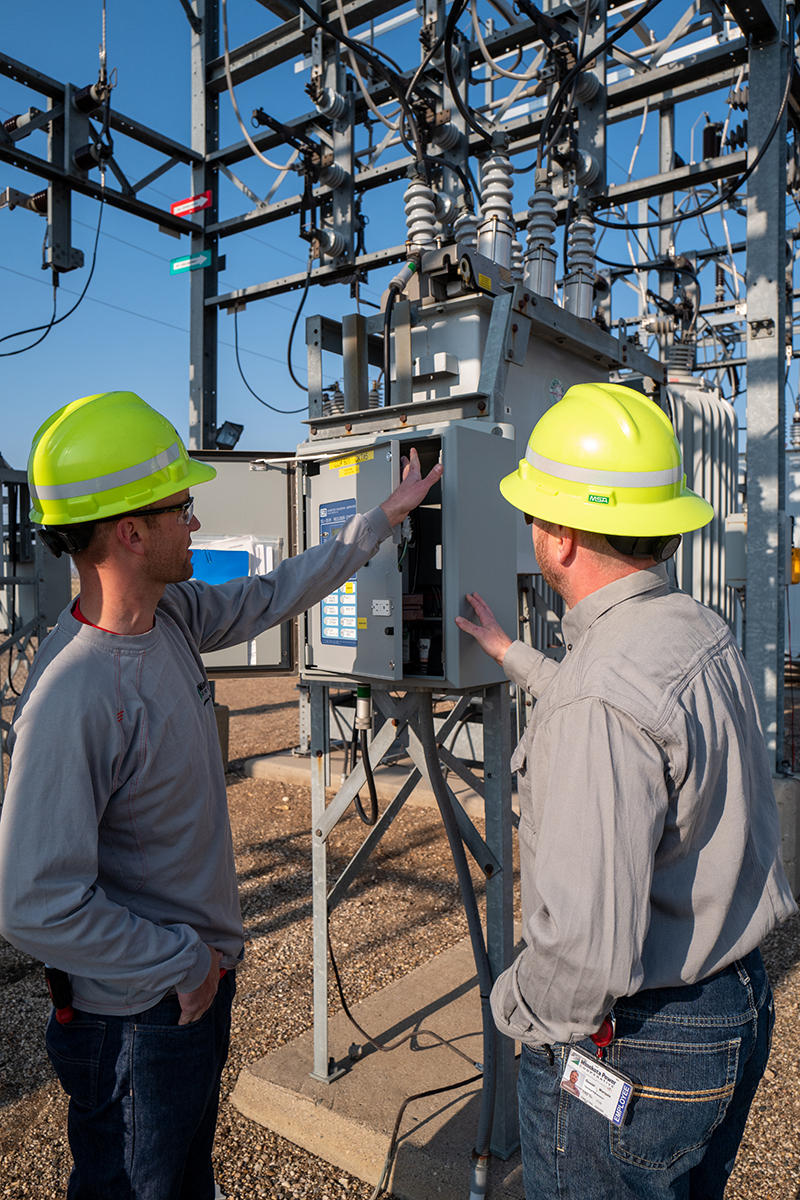
More control in the control center
Within days, System Operations superintendent Reed Daws had already experienced the benefits of Coleman’s DA upgrade from Minnkota’s control center. Some Nodak Electric Cooperative member-consumers were noticing voltage irregularities.
“We could see that happening, so we were able to take care of it as soon as possible,” he said. “It’s just one more tool Minnkota can use in order to give the consumer the best possible service.”
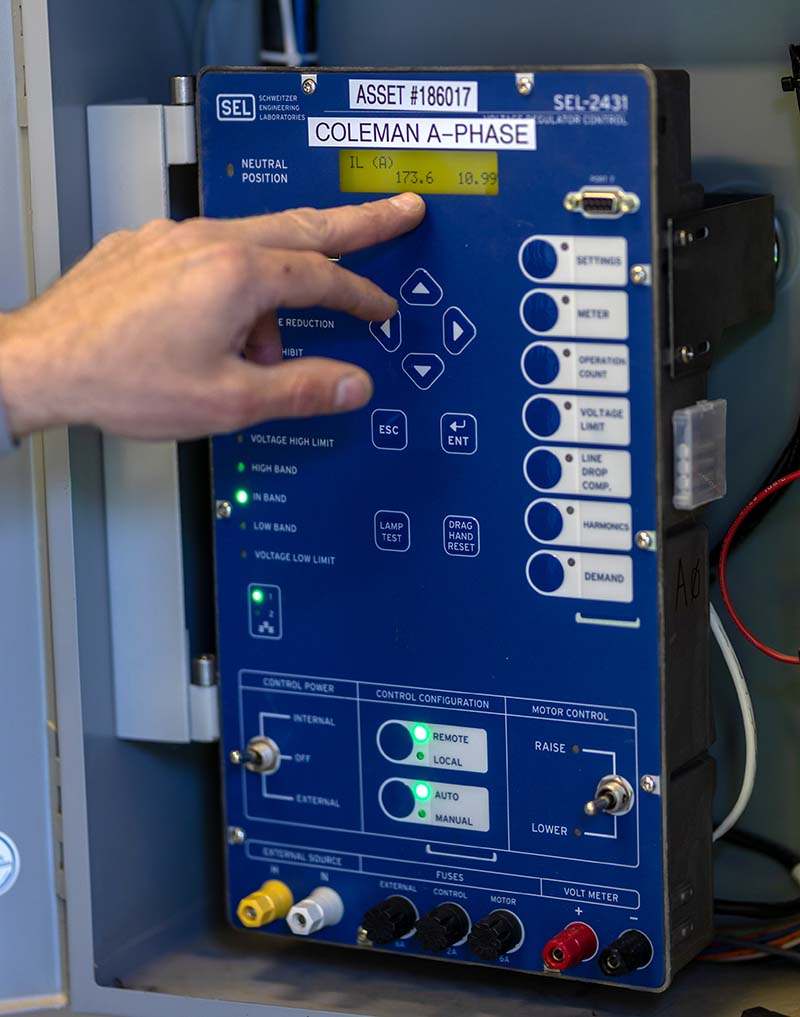
Pointing to his energy management screen, Daws laid out all the areas in which DA enhanced visibility for power systems operators, including more than a dozen alarms indicating high or low voltage, blown fuses, overloads, etc. If a problem can’t be solved by his team remotely – another critical benefit of the upgrade – the specific knowledge of what is happening allows them to dispatch the correct crews to resolve the issue quickly and efficiently.
“Member-consumers are going to see shorter outage times,” Daws said, noting that in the vast majority of fault cases, Minnkota can help get power back to every effected home within minutes. He added that as the DA initiative expands out to the full system, and visibility and remote capability increase, the power systems operators can start to pinpoint problem areas before a consumer knows there’s an issue.
“It’s going to create a more reliable system and safer environment,” he said. “If we deem something is wrong in a sub, we can de-energize it while we wait for someone to get there, and they can go in safely and see what’s going on. Instead of losing high-investment equipment like transformers, we might be able to de-energize them and save them. In the end, it’s going to be very valuable, not only on the financial side, but also keeping people with safe, reliable power.”
Tech coming together
The distribution automation deployment is not only improving response times, but also enhancing the effectiveness of Minnkota’s demand response program. Telecommunications supervisor and planner Wyatt Stramer says the improved data and control has been essential for Minnkota’s new load management ripple monitors, 70 of which were deployed in 2020.
“With all the new DA sites, and having that communication back into the energy management system, we’ve been able to scatter a ton of those ripple monitors throughout our whole footprint. That gives them a better eye on what that load management voltage is,” Stramer said. “That’s the key to the whole system, having that right voltage in the right place to turn things on and off. That is a huge plus.”
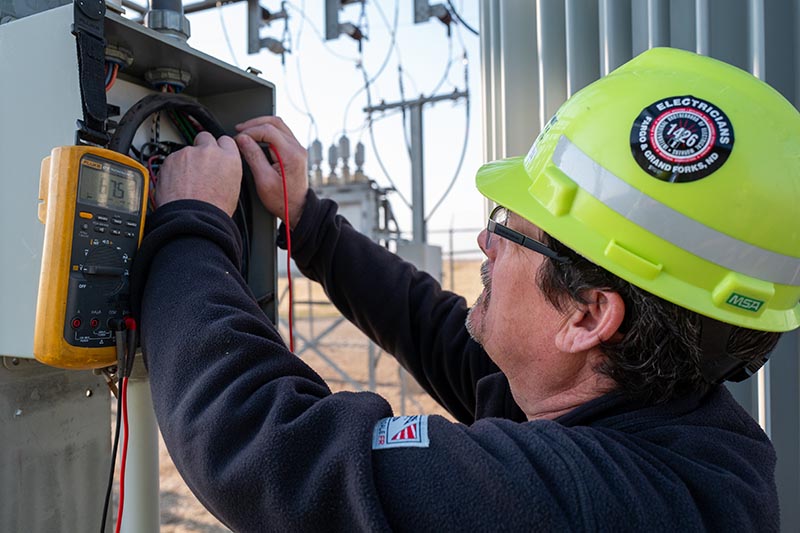
The technology came together just in time, as Minnkota relied heavily on the demand response system to reduce overall load when a February polar vortex event strained the regional grid. Marquis heard from Todd Sailer, Minnkota senior manager of power supply and resource planning, that the new system helped them navigate the weather-based challenge seamlessly.
“He said it was the best that he’s ever seen,” Marquis said. “A lot of that can be attributed to having more information now.”
The distribution automation rollout has been effective because of many advanced technologies converging, requiring close collaboration between multiple departments. But it also takes collaboration with Minnkota’s member cooperatives, whose substation needs now help determine where the next DA sites are planned. As distribution co-op planners experience more of the member benefits firsthand, more requests for site upgrades are submitted.
The many Minnkota teams behind this substation revolution sometimes get lost in the precise day-to-day work, but they’re often reminded by their leaders of the difference their efforts are making in the community.
“Technical maintenance crews know,” Marquis said, reflecting on what the team accomplished over the past three years. “Every once in a while we get positive feedback about DA in a substation, and I make sure to tell them, ‘This is what happened, and this is what the control center saw. Because of this, you possibly saved customers two hours of an outage.’ People got their power back on, or weren’t out of power, because we have that visibility and operational awareness.”
MAIN IMAGE: A group of Minnkota crew members from different teams assemble to help energize the Berg substation on April 16. (Minnkota/Michael Hoeft)
...