The full picture of reliability
Infrared camera technology serves an important role in Minnkota’s multipronged preventative maintenance plan.
In mid-January, Minnkota electrician Mike Howard was spending another quiet, cold morning at a substation just west of Grand Forks, N.D. But instead of the typical drill and pliers he’d have on hand, he was slinging a state-of-the-art thermal imaging camera. Something through his lens was not as chill as it should be – flaring bright yellow on the camera’s digital screen.
“It’s the bottom of the source switch that goes to the regulators. Our regulators are the most mechanical and potentially dangerous parts of the substation,” explained crew foreman Dean Swatlowski, watching as Howard composed a new shot. “Yesterday it was 320 degrees. Today it was 504 degrees.”
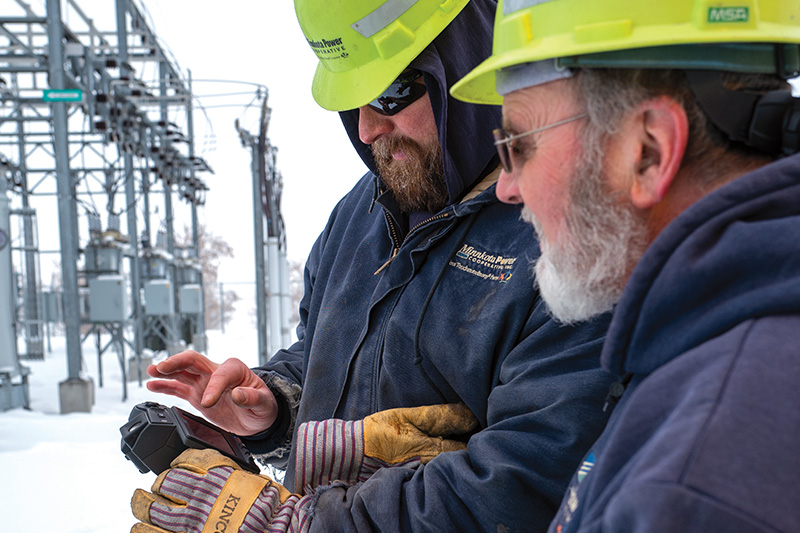
This preventative maintenance scan was the first of a full-system thermal examination of Minnkota’s 257 substations across North Dakota and northwestern Minnesota. Every year, the co-op’s power delivery team schedules time during the cooler months of fall and winter to view every component of each site with a FLIR (Forward Looking InfraRed) thermal camera. If a part of the substation glows more brightly than it should, it indicates a potential issue that could go unnoticed by a standard visual inspection.
In the case of the source switch and regulator, Swatlowski says catching the rise in temperature early may have prevented a failure or even a fire in the months to come. That, in turn, could stave off an outage and keep his crew out of harm’s way.
“The camera definitely helps us to take corrective actions. We can fix the problem before it turns into a catastrophe of some sort,” he said, adding that the camera typically catches one or two system hot spots every year. “It’s a good technology.”
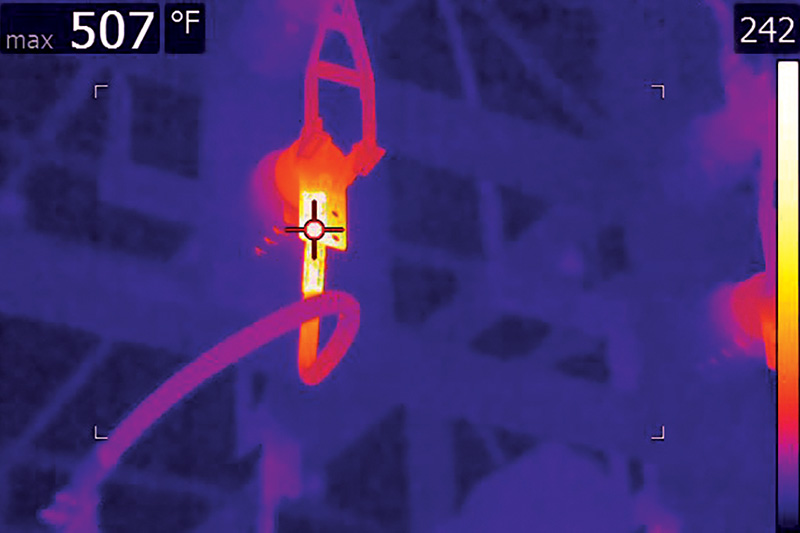
Hot technology
Thermal imaging has come a long way since Minnkota first started using the technology more than 20 years ago. Construction and Maintenance Superintendent Harold Narlock says Minnkota has now used four versions of infrared camera, with the latest FLIR model as the most recent addition.
“They’ve gotten so much better,” Narlock said. “If you come from outside, I can see your footprints walk by in blue, because your shoes are cold. It dissolves right away; you can only see a couple prints as they follow you. That’s how sensitive that camera is.”
Narlock says earlier versions of the technology were limited in what they could see and were quite crude. Minnkota’s first camera actually had a small air conditioner inside to keep it cool and unaffected by ambient temperature. The co-op would only use it to survey a few critical load stations. But as the technology improved and became more user-friendly, its role in strengthening grid reliability grew.
“It was not difficult to use. We put it in the crews’ hands, and we actually started a full-blown maintenance cycle,” he said. “Every year from this point on, we’re going to thermal scan our substations.”
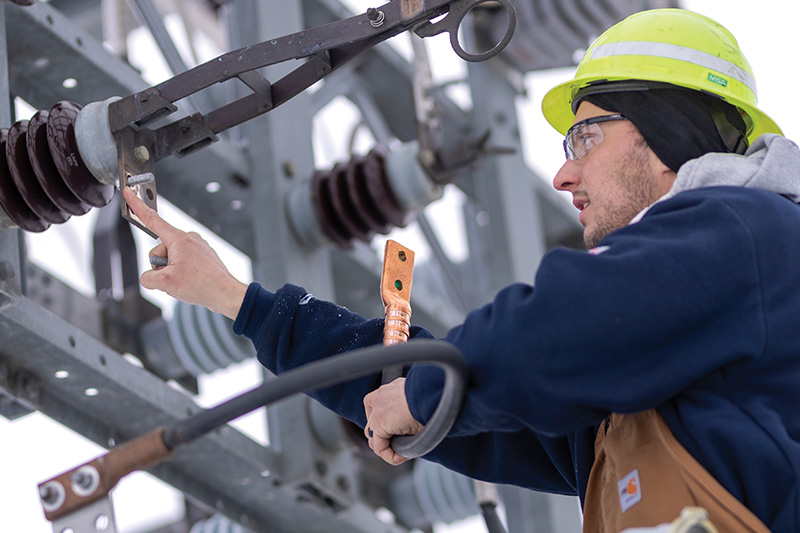
A thermal scan of a substation can detect several potential component issues that generate additional heat, from loose spades to compromised riser leads. If an area appears warm, it doesn’t necessarily indicate an immediate repair is needed. Minor temperature differences are often noted on a “watch list.” If the temperature is trending upward on the next check, a repair is made. Often, watch list items won’t show up on a follow-up scan. Since many of a substation’s components are made of steel that can contract or move in cold, it’s not uncommon in one season to have a warm spot that disappears the following season.
Thermal scans are only one aspect of a multi-department docket of preventative maintenance to minimize outage events. Every one of Minnkota’s power delivery teams is responsible for a different method of annual checks. As electricians run thermal imaging scans, technical maintenance crews test the relays that protect substation equipment, while yet another group completes transformer oil sampling and testing. This is all done to get ahead of any problems that could lead to sudden grid equipment loss, an issue made more complicated with current extensive lead times on industry components.
“If there is a major failure, it can take so much other equipment out at the same time. Plus, you have the risk of there being personnel in the area. That’s a huge safety risk. So, it’s very important to be as proactive as we can,” Narlock said.
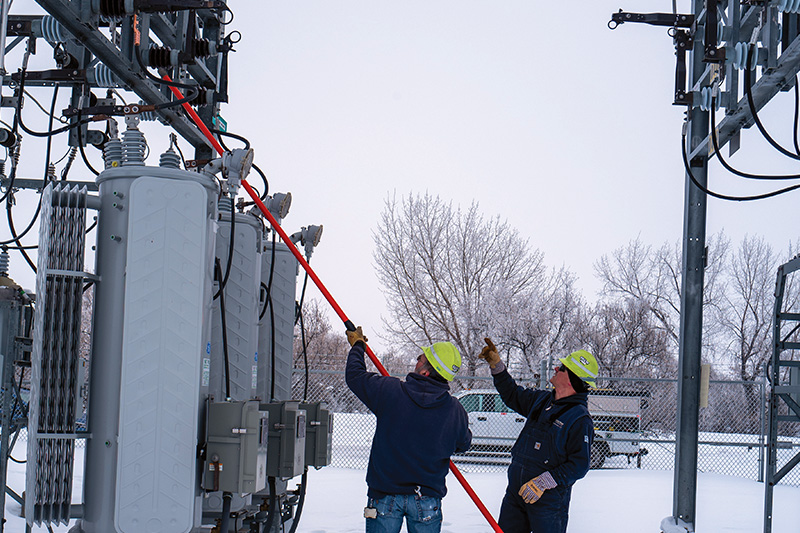
After the FLIR camera was put away for the day, Swatlowski watched his crew of three electricians neutralize the regulators of the substation and change out the problematic switch. A quick look through a thermal imaging device had protected the co-op from a spendy repair, protected member-consumers from a power outage, and protected his team from a hazardous call-out in the future.
“I just want to make sure everyone gets home at night,” he said – with warmth detectable by the human eye.
MAIN IMAGE: Minnkota electrician Mike Howard composes an infrared photo of a substation west of Grand Forks, N.D. (Minnkota/Michael Hoeft)
...